Thought Leadership
Why AI alone can’t save batteries – the case for the grey box
19 April 2023
Introduction
Hardly a day goes by without artificial intelligence grabbing the headlines. Be it in process automation, medical diagnosis, autonomous transportation, language processing or even gaming, applications of advanced machine learning algorithms are ubiquitous. Outside of highly publicised advances such as ChatGPT, machine learning has equally spread across all branches of science and continues to provide a rich source of innovative research work. In this sense, batteries are no exception – AI has become commonplace in fields such as materials discovery and characterisation, optimisation of experimental design and manufacturing, as well as state of charge (SOC) and state of health (SOH) estimation. Given the all-pervasive character of AI/ML in current state-of-the-art battery research, it is worthwhile to take stock and critically assess the added value of these methods vis-à-vis their more conventional counterparts. With all the hype, it can be difficult to see the wood for the trees – where does the value of these ‘black-box’ methods lie? Can their performance in real-world scenarios be expected to match expectations from the sandbox (lab) settings? Here we offer brief insight into the potential benefits of AI/ML based methods in the field of SOH estimation, and highlight where they fall short, ultimately making the case that only through fusion of data-driven and model-driven approaches can we provide robust solutions for real-world battery systems.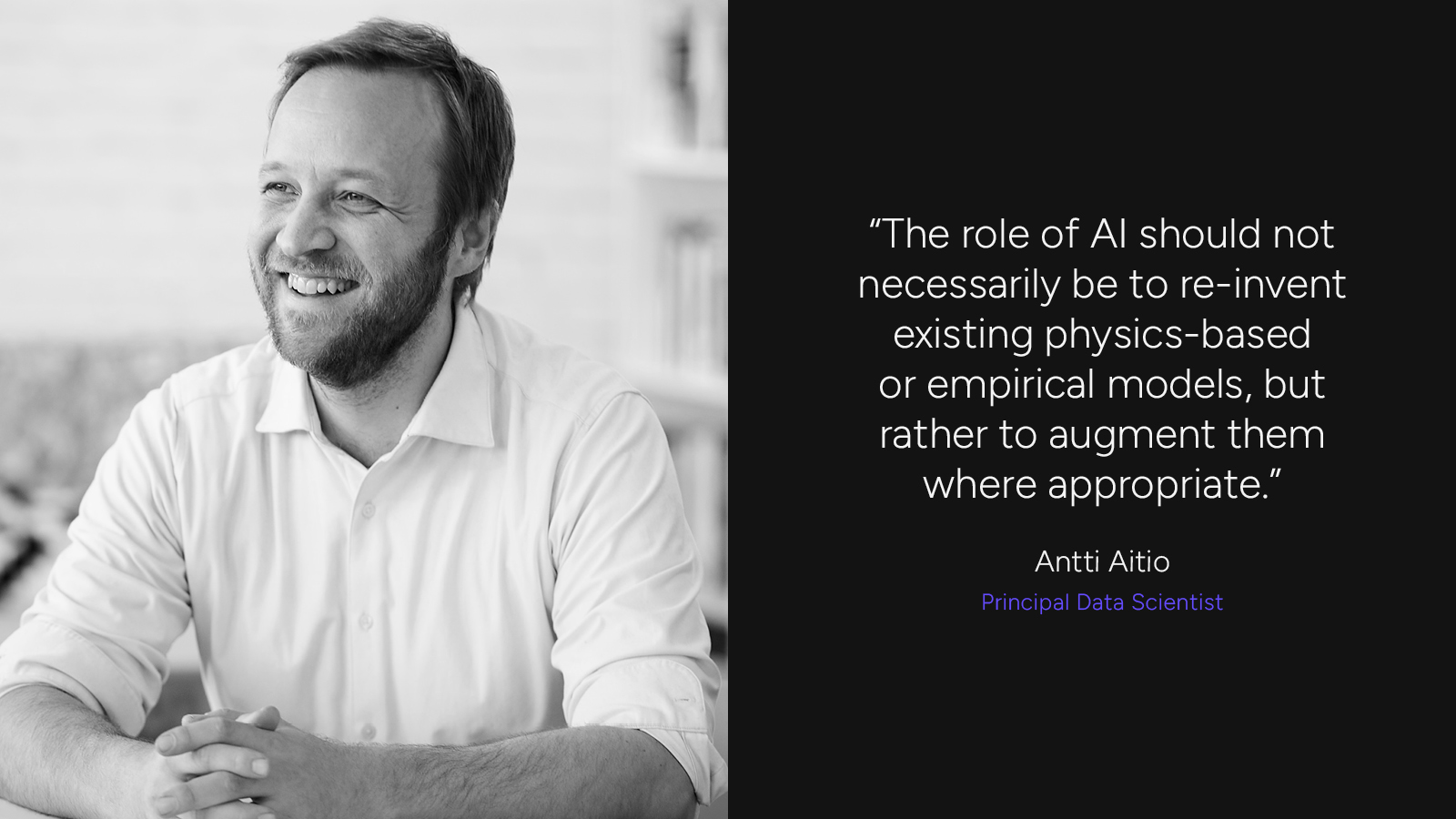
Want to read more?
Tell us a bit more about yourself to access the full article.